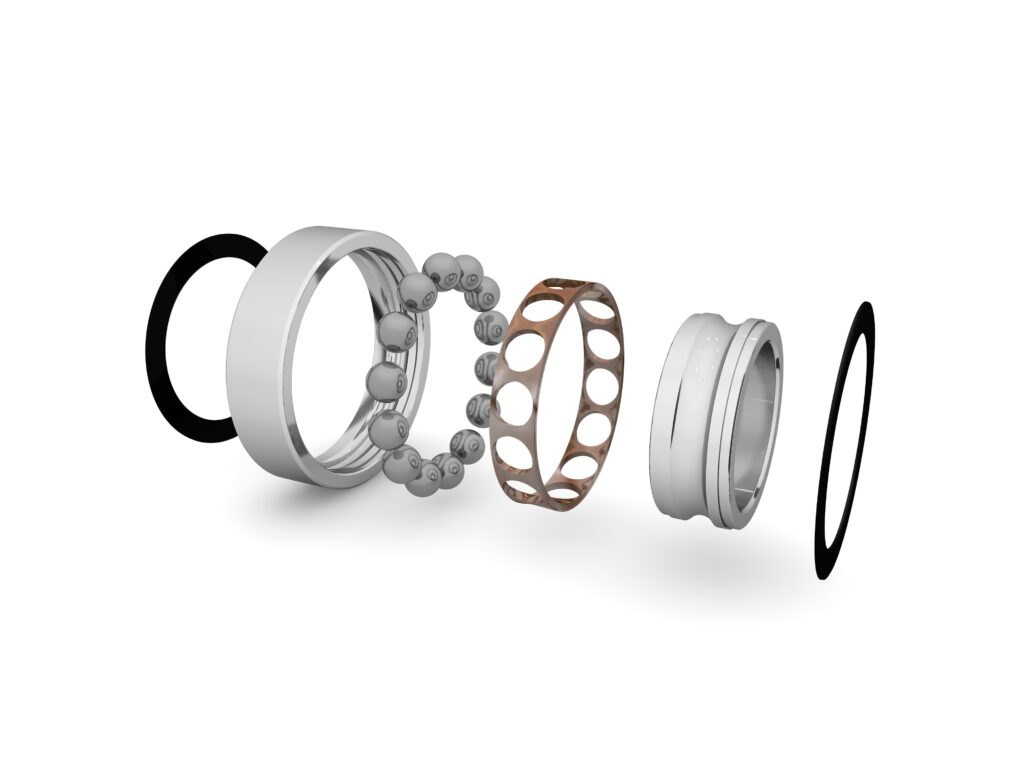
Self-lubricating bearings are revolutionizing the technology landscape, particularly in industries heavily relying on machinery. They can be characterized by their unique ability to transfer microscopic amounts of material to the mating surface. This process of transference creates an efficient film that provides lubrication and effectively reduces friction over the length of the rail or shaft.
The critical aspect here is that self-lubricating bearings demonstrate several advantages over traditional lubricated ones, including saving time and money on preventative maintenance while posing no hazardous waste from lubricant disposal or cleanup. The concept behind these bearings centers around a simple principle – frictional forces should remain consistent without requiring additional grease or oil, which may attract contaminants known to destroy conventional bearings.
Benefits of Self-Lubricating Bearings
One must first comprehend how traditional ball-bearing systems work to understand why self-lubricating bearings are advantageous. Traditional systems demand regular maintenance schedules involving re-oiling or greasing at frequent intervals. The necessity for manual intervention not only accumulates labor costs but also increases downtime during equipment servicing periods.
Conversely, self-lubricating bearings eliminate these constraints as they require minimal human intervention once installed correctly into a system due to their built-in capacity for continuous self-renewing lubrication.
The key lies in how these bearings operate. As the bearing moves along its axis, it naturally transfers small quantities of its material onto the mating surface, creating a thin layer of solid lubricant between moving parts that acts as an effective buffer against frictional wear.
This ingenious mechanism enables two significant advantages; firstly, it drastically reduces maintenance needs because there’s no requirement for regular application of external grease or oil since this ‘lube layer’ continuously regenerates itself during operation (hence ‘self-lubrication’). Secondly, it significantly decreases wear rates because there is always a lubricating film, reducing the risk of failure and extending equipment lifespan.
Moreover, self-lubricating bearings have an ecological advantage. Traditional bearings often require petroleum-based lubricants, which can be hazardous to the environment if improperly disposed of. However, self-lubricating bearings eliminate this issue entirely by not requiring any external lubricants – thus generating zero waste from lubricant disposal or cleanup. This eco-friendly aspect is particularly beneficial for industries striving to align their operations with sustainable practices.
In addition to environmental benefits and cost savings on maintenance and labor, these innovative self-lubricating technologies offer exceptional performance advantages over traditional bearing systems. They provide consistent frictional forces on the bearings and drive system throughout their operational lifetime – ensuring optimal machinery performance without any decline due to wear or contamination.
Furthermore, these high-performance bearings are resistant to various contaminants, such as dust particles, that may infiltrate traditional systems, causing premature wear and shortening bearing life spans. The absence of grease or oil in a self-lubricated system reduces contaminant attraction, providing additional protection against premature wear.
Another great advantage lies in their versatility; self-lubricating bearings can be used across a wide range of applications – from heavy-duty industrial machinery to precision instruments where reduced friction is crucial for optimal functioning – making them an ideal solution across diverse sectors including automotive manufacturing, aerospace engineering, construction equipment production among many others.
The Future
Interestingly enough, research continues refining this groundbreaking technology further, with several studies focusing on potential enhancements like improved heat dissipation properties or increased load-bearing capacities that could make self-lubrication even more efficient.
The future holds exciting prospects for this emerging technology as it continues to gain traction within various industry sectors, looking for effective ways to reduce maintenance costs while enhancing efficiency and sustainability concurrently. With ongoing advancements in materials science and engineering techniques explicitly related to these novel bearing system types, we anticipate significant leaps forward in the coming years.
In conclusion, self-lubricating bearings are an innovative technological advancement that offers multiple benefits, including reduced friction, minimal maintenance needs, and zero waste generation. This technology is not only saving industries valuable time and money but also making a positive impact on our environment by eliminating hazardous waste. The future of bearing technology lies with self-lubrication – a sustainable, cost-effective solution to redefine machinery operation across numerous sectors.